2023
Engineered Wax Emulsion for Wood Composites
Description:
The WVCO Engineered Wax Emulsion enhances two key industry interests: Safety and Cost. The Engineered Wax combines bio-polymer and wax chemistries in a patented process to achieve novel wax properties. This emulsion is designed to be inline mixed, and co-applied with, pMDI during wood composite production, allowing significant pMDI reduction (>10%). Furthermore, wax volatility is suppressed (i.e., flash point increased ~50°F), thereby reducing wax deposition outside press, reducing fire hazards.
2022
Flamex, Inc.: MXOne High Performance Fire Protection Turbine
The MXOne has a 360° operating range and enables the highly precise application of water mist from a significant and safe distance. When applied to a fire, the water mist absorbs a huge amount of energy, cools particularly effectively and reaches hidden fire sources better than typical water spray devices.
MXOne can be operated with potable water, seawater and with/without foaming agents. Spray patterns can range from a fine water mist to a full jet. It can produce a flow rate of up to 4,000 liters per minute. MXOne can be aimed at a hot spot either fully automatically or manually via remote control. Thanks to a smart operating system, a single turbine can supply water alternately to two or more neighboring areas. Accordingly, several fires can be fought in parallel, or nearby facilities threatened by fire can be cooled to prevent ignition.
The turbine can be easily integrated into existing plant facilities and is suitable for use in areas with temperatures ranging from -25°C to +60°C.
2021
Arclin: HP600+ Resin System
The HP600+ technology combines our Fast Cure Resin System and Low Spread Technologies to produce a “super resin” that significantly reduces spread rates and hot press cycle times, all without a corresponding reduction in dry out tolerance. It reduces hot press cycle times by 5% to 15% on average, increasing mill throughput and reducing unit production costs on press-bound constructions. It also reduces adhesive spread rates by 8% to 15% on average, reducing applied adhesive costs and incrementally improving tolerance to elevated veneer moisture content.
Several mills converted to the Arclin HP600+ technology in 2021. Those mills, on average, have recognized a panel throughput improvement of 9.8% with a glue spread rate reduction of 8.0%, all while sustaining or improving on-grade.
2020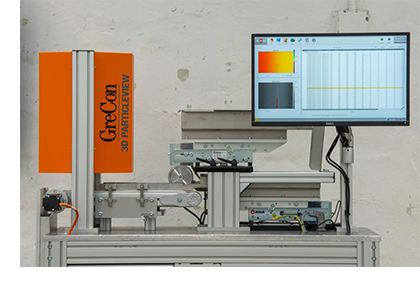
Fagus GreCon: 3D ParticleView
The 3D ParticleView is a measuring unit that assesses the wood particle quality. The particles are taken from the process downstream of the knife ring flaker and are placed in the particle view. The unit will use a patented laser line and camera to measure the length, width and thickness of each particle.
The particle thickness is an important parameter for the physical characteristics of finished particleboards. The ratio of particle surface to volume is the most important variable in glue application. The surface and volume of the particle both depend on the adjustment of the knife ring flaker and these variables can change as the knife ring takes on normal wear and tear.
2019
KTC Industrial Engineering, Nova Robotics: OSB Press Platen Repair Robot
Presses accumulate wear and require regular maintenance, but it is rarely economical to schedule a full maintenance shutdown for minor repairs. Human labor cannot be performed on or around a hot press. As a result, maintenance is deferred to infrequent, often annual intervals during large scheduled maintenance shutdowns. This limitation frequently results in the decision to continue plant operation even though board quality and output are diminished.
The OSB Press Platen Repair Robot is a high-temperature OSB Press Repair Robot capable of repairing press dents by welding and grinding. Robots can be sent into a press and perform work immediately and at full press temperature. Platen surface damage due to rocks and metal debris may now be corrected immediately after it occurs. It is no longer necessary to defer necessary work to scheduled cold shutdowns. Costly maintenance may now be performed as required to restore full operational performance while improving safety by keeping people out of a dangerous environment.
2018
Arclin, Enhanced Bond Technology
When the veneer is dried too fast at too high of a temperature, the chemistry of the wood surface is modified, restricting the ability of water - and the PF adhesives common to plywood manufacture - to adequately absorb and penetrate beyond the veneer surface. The result frequently observed is shallow and spotty wood failure, reduced strength, and increased panel downfall due to delaminations.
Resins incorporating the Enhanced Bond Technology cut through the chemically modified veneer surface to improve adhesive flow and penetration and to increase the depth and consistency of wood failure when gluing overdried veneer. A second benefit observed with Enhanced Bond Technology is improved wood failure in areas that are notoriously difficult.
The transition to an Enhanced Bond Technology resin is seamless for the user. There are no additional raw materials to purchase and handle, the SDS is consistent with a typical PF resin, and it requires no changes to the storage, mixing, or panel layup process.
2017: TIE
Sweed, Vacuum Feeder Peel Cups
Sweed’s new patent-pending “Smart Pause” technology provides veneer dryer infeed operators additional time to address veneer feeding issues while maintaining a 100% dryer fill rate. This is accomplished without stopping the dryer, thus maximizing production. Sweed’s “Smart-Pause” Infeed functions separately from the veneer dryer, utilizing the latest innovation in infeed programming and driving each deck independently. Smart Pause allows the operator to pause the feeder for up to 20 seconds upon a misfeed without stopping the dryer. Once the misfeed is corrected, the “Smart Pause” infeed allows the veneer to “catch up,” and eliminates the gap created from the pause. Primary and Secondary Stop-Gates on each deck assures a veneer lap occurs prior to veneer entering the dryer. This technology virtually eliminates feeder misfeeds and helps to improve veneer presentation to the dryer. Sweed’s “Smart-Pause” Dryer Infeed is a proven solution and increases overall dryer efficiency and production. It is the highest-producing dryer infeed available in the industry today.
USNR: Cross Laminated Timber Press
USNR’s new modular press for the manufacture of cross-laminated timber panels features key design elements for the emerging North American CLT market. A key difference in USNR’s press is the use of compressed air instead of hydraulics. The panels are assembled using between three to seven layers of cross-laid timbers. The adhesive is applied between the layers prior to the panel entering the press. This press follows a “window frame” design consisting of 20 identical steel frames spaced 18” apart, with each frame having an opening (or “window”) which allows CLT panels to pass through the press. Once the panel has been fed into the press via a set of pop-up rolls, it comes to rest on platens within the press opening. A set of pneumatic cylinders then applies pressure from the sides to ensure minimal gaps between core materials within a given layer. Meanwhile, a set of channels carrying 8 large diameter pneumatic hoses is lowered to rest on top of the CLT panel. Once the panel is configured correctly within the window of the press, the 8 hoses are brought to pressure (typically to 100-150 psi). Press time depends largely on the time it takes to lay-up the panel, with a ratio of approximately 2.5:1 (press time to lay-up time). The unique curvature of USNR’s press opening allows it to redistribute the stresses and withstand the tremendous pressures required to produce APA-certified CLT panels. While most CLT presses utilize hydraulic cylinders to achieve the necessary pressures, the USNR press applies pressure pneumatically instead. This method is robust, extremely cost-effective, and more environmentally friendly than the hydraulic alternative. An additional advantage to the USNR design is its modularity – it can easily be modified to any desired length by simply adding or removing window frame segments.
2016
Willamette Valley Company, Will-Spray 500 adhesive
Wil-Spray 500 is a water-based, odorless spray adhesive eliminating the need for staples/hot melt to affix overlays to veneer in the matching process. A superior bond between the overlay and veneer is achieved with a larger bond area reducing overlay damage during layup process.
Wil-Spray 500 is currently used on manual matching stations for overlays. Customers have quantified increased production, reduced fall down, and reduced product cost associated with this product. Automation has been developed for this process using spray guns and automatic spray systems.
Product benefits:
- Eliminating strenuous and repetitive actions (manual staplers)
- Superior bond with a greater bond area
- No bleed-through or negative effect on the bond line
- Improved efficiency through the application of product (increased production)
- Reduced fall down associated with overlay damage during the layup process
- Reduced labor cost through the automating process