Innovation of the Year Entry A
ARGUS Smart-Connected Technologies
Entered By: Kadant Carmanah
Date of First Use: May 2023
Benefit 1: Prevents unscheduled downtime at the strander with condition monitoring and analysis in real-time.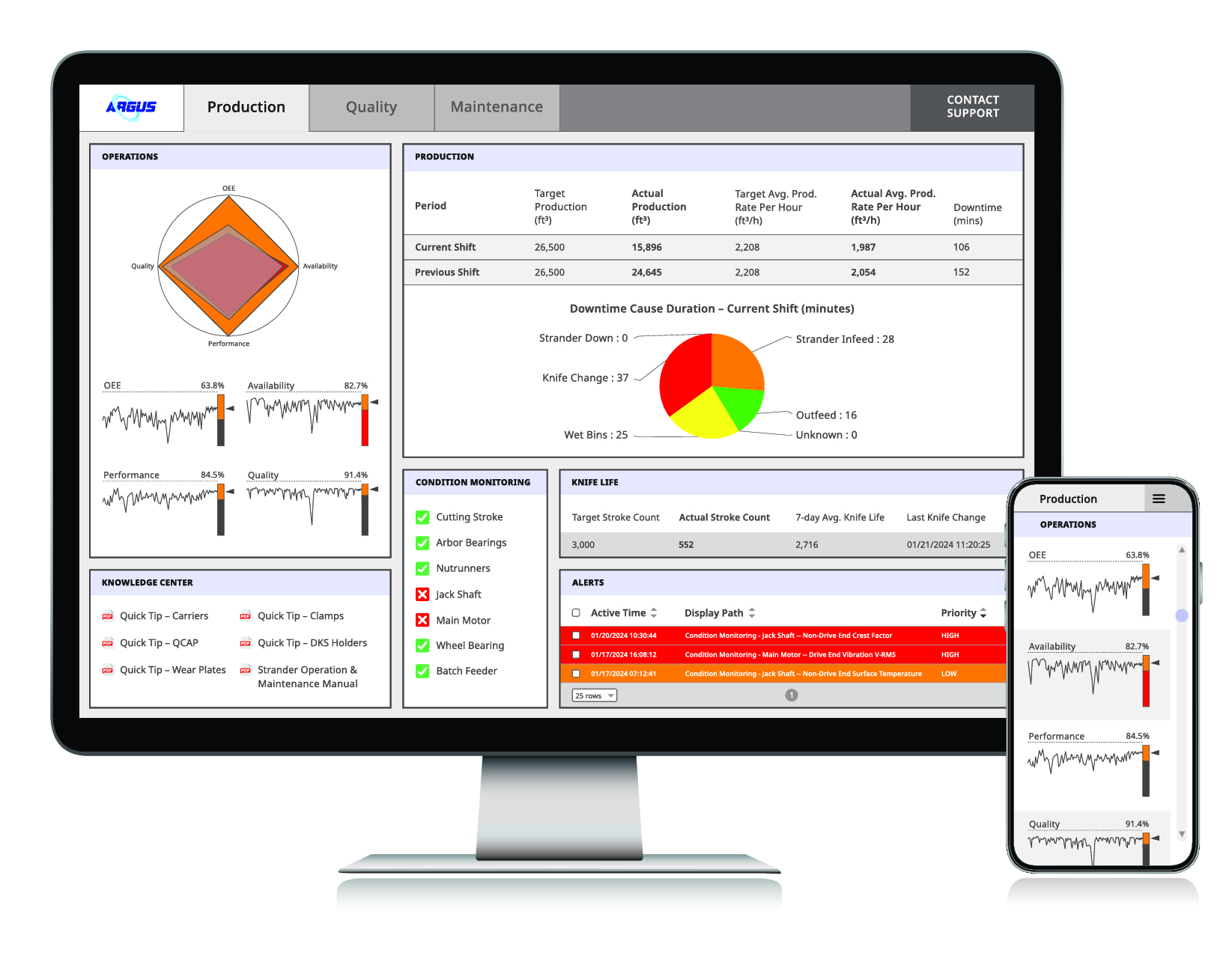
Benefit 2: Monitors strand quality, improves throughput, and reduce strand deviation in real-time.
Measurable results from case studies:
1. Within the first three months of the first pilot installation, the ARGUS Condition Monitoring & Intelligence (CMI) system prevented eight hours
of unscheduled downtime by identifying a failing bearing related to excessive drive belt tension. The mill was able to replace the bearing on a scheduled down day and correct the belt tension to prevent further failures.
2. At our second pilot installation, the ARGUS Fines Measurement System (FMS) was installed at the strander outfeed, green screen discharge and blender infeed. The mill can track strand degradation throughout the entire process and now has the ability to fine-tune resin and wax application to match the fines percentage in real time.
Description: ARGUS Smart-Connected Technologies combines and analyzes data from our proprietary vision systems, an array of condition-monitoring sensors and existing PLC tags to provide OSB producers with data-driven insights about how their strander is operating in real time. Live dashboards and reporting delivers accurate trending for Overall Equipment Effectiveness (OEE), with the ability to benchmark strander performance across multiple operators, shifts and/or lines.
Additional Details:
ARGUS Smart-Connected Technologies was developed by Kadant Carmanah, to provide OSB woodroom operators and management with the data they need to produce better quality strands at higher production rates, while preventing unexpected downtime at the strander. This innovation combines 3 different proprietary systems to deliver the metric for Overall Equipment Effectiveness (OEE) at the strander, so that OSB producers can make more informed decisions about how to optimize the productivity of their stranding operation in real-time:
System 1: ARGUS Log Fill Optimizer (LFO) – this is a vision system that scans the log fill level at the strander infeed, measuring the amount of wood the strander consumes in real-time. OSB mills can now modify their infeed for higher fill rates, increased throughput, and improved operational efficiency. The ARGUS LFO unlocks the OEE metric for Performance.
System 2: ARGUS Condition Monitoring & Intelligence (CMI) – this is a series of condition monitoring sensors that have been installed across all strander components and assemblies, to collect and analyze data-driven insight about how the strander is operating in real-time. OSB mills can now identify bottlenecks at the strander and detect equipment anomalies in real time, and take immediate action to avoid unexpected downtime. The ARGUS CMI unlocks the OEE metric for Availability.
System 3: ARGUS Fines Measurement System (FMS) – a vision system that continuously scans the strander outfeed conveyor to provide real-time fines percentages for every cutting pass. Automating the strand sampling process in real-time removes the variability and bias associated with inconsistent and infrequent strand collection procedures currently done manually. With access to a far greater number of accurate strand samples, OSB producers can now make more informed process improvement decisions in real-time. The ARGUS FMS unlocks the OEE metric for Quality.
Innovation of the Year Entry B
Nicholson MLX (3D printed) Debarking Tips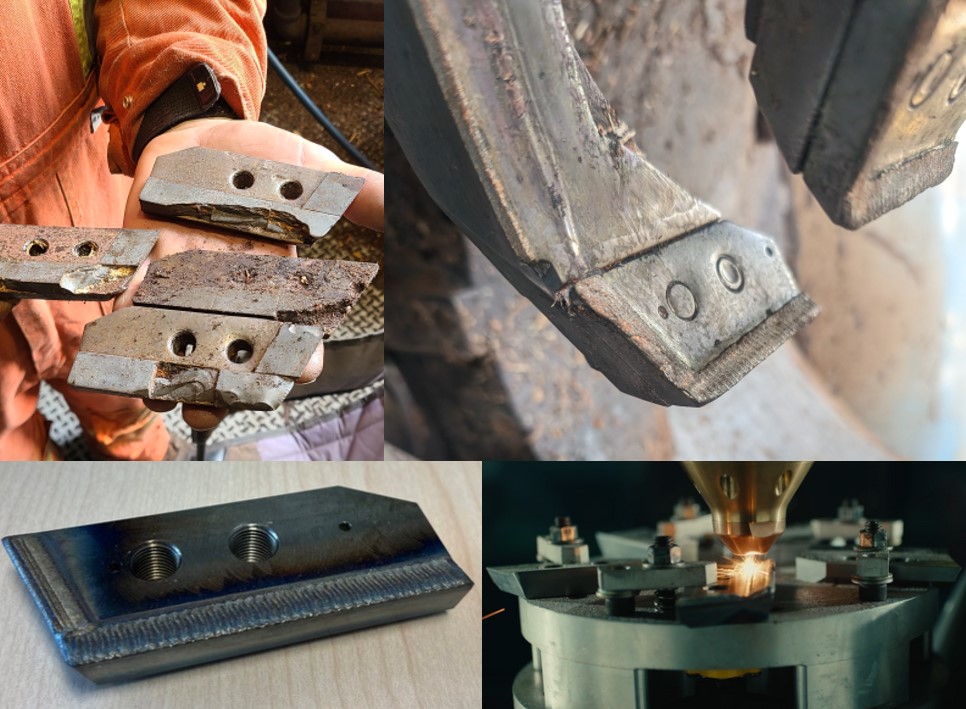
Entered By: Nicholson Manufacturing
Date of First Use: August 2023
Benefit 1: Increased impact and wear resistance.
Benefit 2: Reduced maintenance and downtime.
Results: Old tips, which would be destroyed in a week or less from rocks, etc., now last 6-11 weeks.
Description: Additive manufactured (3D printed) self-sharpening debarker knife tips replace sintered carbide tips. Nicholson developed a proprietary formula, providing up to 25% increased wear life and up to 10x increased impact resistance. Less maintenance, more uptime, lower cost to run. Results vary depending on the application.
Additional details:
Our new patent-pending self-sharpening MLX knife tips have now been field tested to wear as well or up to 25% better than carbide tips, depending on the log species, condition, etc. Nicholson has developed, in-house, a proprietary formula for our additive manufacturing process allowing us to "3D print" the tool edge onto the tip blank.
Besides longer wear life, the real game changer is the impact resistance. Mills that have debris, such as rocks stuck in the bark, often destroy their carbides. This particularly affects coastal mills, and some mills say they can destroy a tip a shift.
One of the customers running the new MLX tips said that knife tips are no longer considered a maintenance item, and they have set new records for uptime and production levels. This new process will be introduced and utilized across our range of maintenance and wear parts.
Innovation of the Year Entry C
Compact Lay-up Line
Entered By: Raute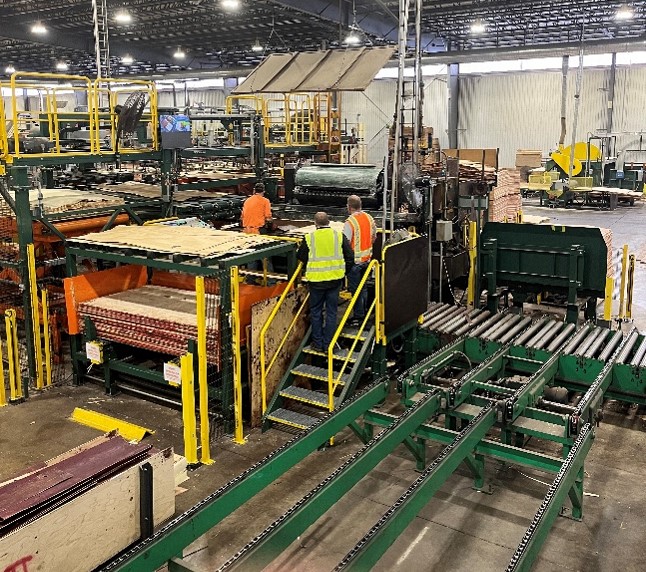
Date of First Use: March 2024
Benefit 1: Partial automation benefits without the space and cost of a new automated lay-up line.
Benefit 2: Reduction of labor: The client was continuously burdened with labor shortages. The new line allowed them to reduce spreader labor by six people while maintaining production levels.
Results: In just three months, the customer has realized a 9.4% reduction in labor costs (in the spreader department) with output remaining the same = increase in productivity per man-hour. The customer has already put in another order after three months of results.
Description: The compact lay-up line is approximately 50’x40’, while traditional lines are 100’+. This line was developed for those customers who still use roll coaters as opposed to curtain/extruder or spray booth lay-up systems. This is a labor-intensive process, and these mills do not have space for typical automated lay-up lines of 100’ or longer. This solution allows mills to take advantage of their existing roller spreader while adding automation to part of the lay-up process.
Additional details:
What is unique about Raute's compact lay-up line solution is that it automates a spreader, performing the task of two personnel who normally carry a sheet over a laydown operator. The mill can reduce their labor count while maintaining productivity levels.
Traditional lay-up lines are of a much larger scale (100'+) and utilize a different glue application method. This line is approx. 50'x40', so it saves space and offers automation without the cost of a full new system.
Innovation of the Year Entry D
A water-based MDI suspension for reduced MDI resin consumption in the wood-based panel sector
Entered By: SMARTECH Manewfacturing 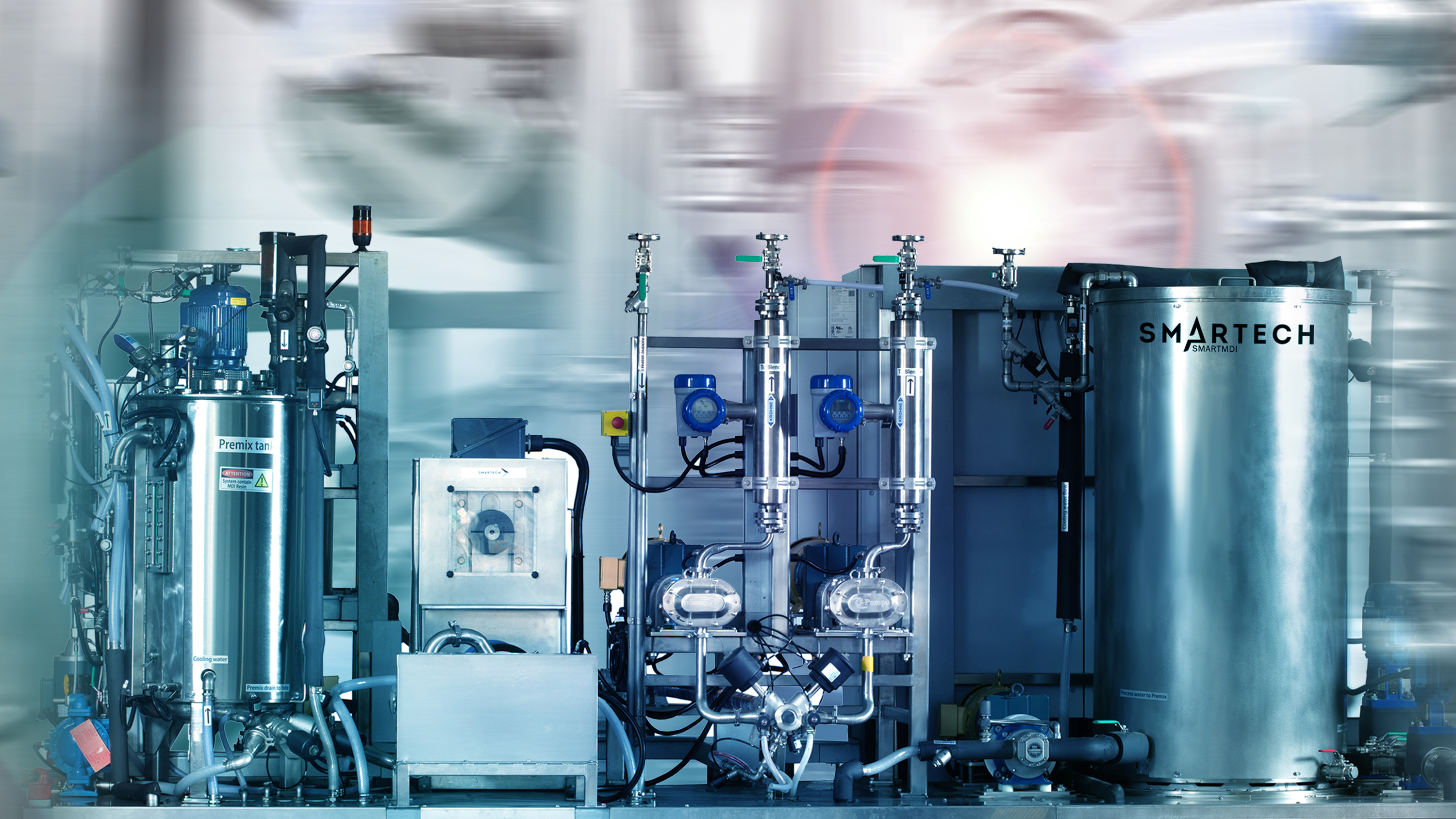
Date of First Use: February 2024
Benefit 1: Reducing wood-based panel production costs while increasing panel quality properties.
Benefit 2: Greener product: Lowering the airborne concentration of MDI during production.
Results: 15% reduction in MDI use while maintaining panel performance.
Description: The novel SMARTMDI System delivers a water-based methylene diphenyl diisocyanate (MDI) suspension for the wood-based panel industry. The System generates an oil-in-water suspension of MDI as a substitute for neat MDI, known as the best-performing formaldehyde-free wood binder. The technology overcomes the premature and unwanted reaction between water and MDI with an additive and specific process conditions.
Additional details:
MDI is the best performing wood binder having no formaldehyde emissions, it's well-regarded in the wood-based panel sector for improving the manufacturing efficiency of oriented strand board, chipboard and fiberboard. Many wood-based panel manufacturers are interested in expanding its use in their facilities but are reluctant to do so because it is costly and subject to supply constraints. Lowering these barriers would accelerate further adoption of MDI. End products utilizing MDI won't have a deleterious effect on indoor air quality in the home or office compared to other formaldehyde-emitting boards.
SMARTMDI is the unmatched solution for the reduction of MDI resin by at least 15% in the manufacture of wood-based panels. SMARTMDI enables a lower MDI resin load for a greener product while maintaining strict quality standards. With a short ROI, SMARTMDI boosts plant profitability and contributes to sustainability targets.
SMARTMDI generates a water-based MDI suspension in real-time where the water functions as a dispersion medium, viscosity modifier and promoter of surface binding. Despite common knowledge that water triggers the reaction of MDI, SMARTECH has successfully developed a multi-pronged method to slow the reaction until the MDI suspension is distributed to the target substrate.
The MDI suspension is delivered with a controlled droplet size resulting in a significant improvement in resin distribution upon the wood substrate and improved MDI reactivity. This enables a reduction of at least 15% of MDI resin while providing equivalent performance to the final wood-based panels. SMARTMDI integrates directly with existing production lines and allows manufacturers to reduce formaldehyde content aligned with regulatory and sustainability goals.
Innovation of the Year Entry E
Green Veneer Squeezer Press
Entered By: SparTek Industries
Date of First Use: July 29, 2013 (prototype machine)
Benefit 1: Improves usability of veneer; reduces waste in dry end operations.
Benefit 2: Reduces dryer time; enables increased production capacity.
Results: A 15% (conservative) throughput capacity increase of dry veneer through the dryers.
Description: Uses pressure and position control to migrate water out of saturated pockets located in green veneer and distributes the moisture evenly across each sheet. Average moisture is then a better indicator of moisture content across the full area as opposed to an average to reduce the amount of re-dry wood creating more waste and
brittle veneer. By reducing water pockets, the overall moisture content of a veneer sheet can be increased while not increasing re-dry, resulting in a higher quality product.
Additional details: (Information provided by Andy Frei of Frei Consulting, LLC (frei.consultingllc@gmail.com):
Testing and use were primarily performed on Hybrid Poplar Veneer. Species, climate, season, and processing method are all variables contributing to varied results. A typical 4'x8' x 28" high load of hybrid poplar would yield up to 120 pounds of water released during the Spring and down to 0 pounds during Winter. De-watering can be a bonus effect from the pressing cycle, however the equal distribution of water is the main goal. Initial testing was performed at the University of British Columbia which verified the water pockets would move from the original cells and indicated optimum time to dry would be less than two hours after squeezing. After the two-hour window from time of squeezing, the water would migrate back to the original cells but still had some value up to 12 hours. After 24 hours, the remaining water would return to its original cells. Testing pressure of load was accomplished using a hydraulic press with varied pressures and times. A nominal load of green veneer 4'x8' stack was subjected to pressures varying from 50-200p.s.i. Deformation of the green veneer can be a concern given the specie and applied pressure. We found detrimental deformation to occur at almost twice the textbook value in certain species. When defamation did occur, typically to the top 3-5 sheets, the veneer would rebound during drying and thickness variation was minimal. For testing before and after movement of water pockets, a Mecano Moisture Volume Analyzer (MVA), using microwaves, displays a moisture map for the sheet is used. SAP sorted veneer using this process saw the largest benefit from moisture migration.
The production grade Green Veneer Squeezer Press designed and manufactured by SparTek Industries has been tested and proven to equalize water distribution through stacks of veneer without significant damage to the material.
Innovation of the Year Entry F
KP-14 Vapor Permeable Barrier Coat
Entered By: The Sansin Corporation
Date of First Use: May 2024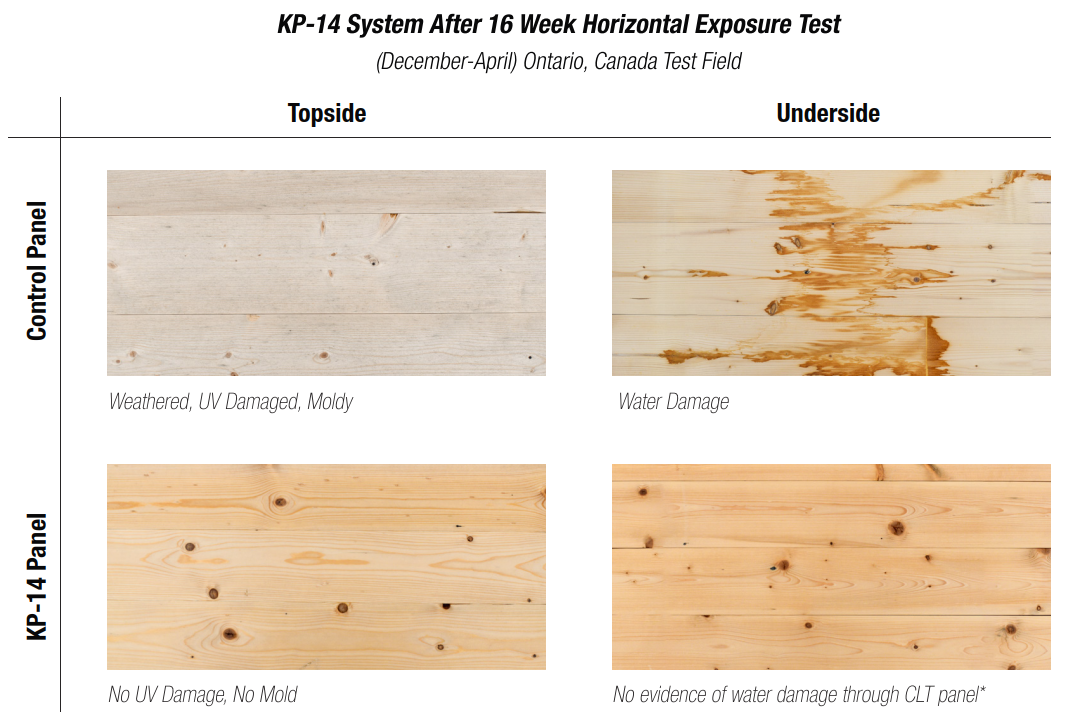
Benefit 1: KP-14 is a vapor-permeable barrier coating that acts as a barrier to hold water out similar to a traditional rubber membrane. KP-14 is a low-VOC, water-borne, environmentally friendly coating that is more sustainable and more affordable than traditional rubber membranes.
Benefit 2: Benefit 2: KP-14 allows for water vapor to escape the wood, helping prevent mold and wood rot.
Results: KP-14 reduces water absorption by 85% . The KP-14 system has a vapor desorption efficiency of 90% comparable to the 92% efficiency of bare wood conforming to EN927-5 and EN927-4 moisture absorption testing standards.
Description: KP-14 is a water-borne vapor permeable barrier coating for engineered wood components like CLT that is designed to aggressively reduce moisture absorption and weathering in the construction phase. KP-14 is ultra-low in VOCs and can be seen as a more sustainable barrier coating to the traditional rubber membranes used. To achieve best results, KP-14 should be used in conjunction with KP-12W. KP-14 can be factory or field applied.
Additional details:
Sansin has developed KP-14 as a product for engineered wood components like CLT to aggressively protect from moisture absorption and water damage. Traditional rubber membranes can trap moisture, causing mold and wood rot. KP-14 is designed as a moisture protection plan in conjunction with KP-12W for the exposed top sides of CLT panels. This system aggressively protects wood from water absorption while maintaining vapor permeability similarly to bare wood according to EN927-5 and EN927-4 moisture absorption testing.
The KP-12W / KP-14 system offers vapor absorption desorption efficiency of 89% comparable to 92% efficiency of bare wood. This distinguishes KP-14 from other membranes. KP-14 is highly durable and like most Sansin products is water-borne and low in VOCs. Architects, engineers and mass timber manufacturers are often plagued with moisture management challenges, and KP-14 addresses the challenge of water damaged wood. KP-14 holds water out similarly to a traditional rubber membrane while allowing the wood “breathe.”
Innovation of the Year Entry G
Stainable Patch: A bio-inspired polymeric wood repair solution
Entered By: The Willamette Valley Company
Date of First Use: August 2023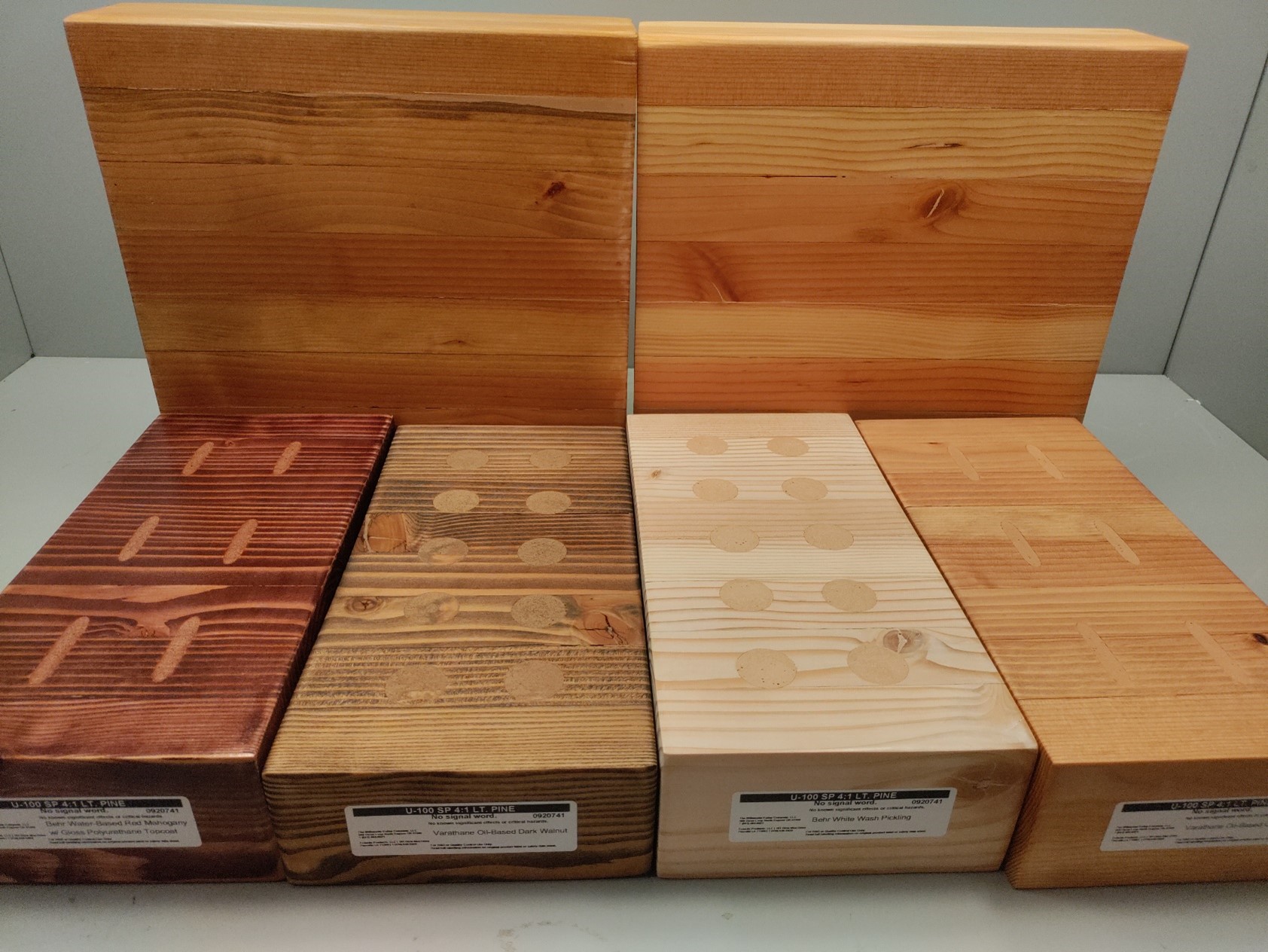
Benefit 1: Enhanced stainability and weathering that is similar to wood substrate minimizing color differential between patch and substrate.
Benefit 2: High biobased content, between 10 and 70%, depending on the application, without compromising performance and stability.
Results:
≥10% reduction in pMDI while maintaining panel performance; About 50 °F reduction in wax volatility
Description: Application on plywood, LVL and CLT showed smooth application, excellent stainability and weathering performances. The Stainable Patch tracked the surrounding wood color 97% better than the traditional poly patch. The product passed all the APA tests to meet the highest quality standard.
Additional details:
WVCO’s Bio-inspired Stainable Patch exemplifies our steadfast dedication to value-driven research, environmentally conscious innovation, and exceptional customer support. We have elevated industry-leading polyurethane and epoxy defect repair products by enhancing their stainability and wood-like weathering characteristics. This advancement not only retains the superior bonding and adhesion qualities of our existing patching products but also incorporates a significantly higher proportion of bio-based components, making it an environmentally superior choice. Key properties include:
• Exceptional adhesion to wood.
• Passes the 2-cycle boiling water test.
• Compatibility with auto-patch lines.
• Manual application for epoxy, consistent with existing epoxy patches.
• Customizable to meet specific customer needs.
• Accepts both oil and water-based stains.
• Weathering characteristics that blend seamlessly with the surrounding wood, ensuring aesthetic appeal.
• Alignment with sustainability and "Green" goals.